How to form veneer
- HOME
- How to form veneer
Process of turning bamboo into materials and products
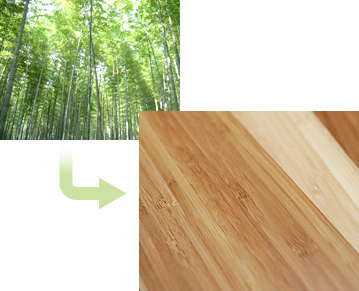
How do you make something like this out of that thin cylindrical
bamboo? I often get asked this.
Bamboo has nodes, and there are also cavities between the
nodes. Due to its characteristics, even the thickest part does
not exceed several tens of centimeters like wood.
How are plate-like and thin sheet-like veneers made from these
properties of bamboo? It seems to stimulate the intellectual
curiosity of the general public.
As a result, we often receive reports from the companies we
deliver to that “customers ask us more about the material of
the display shelves than about the product.”
In this way, bamboo material has an attractiveness and
topicality that attracts people.
Here, we would like to introduce the process from the time
bamboo is felled to the time it is turned into materials and
products.
1.Logging
Use 3rd to 5th grade Moso bamboo.
2.Rough cut
Divide the cut bamboo according to its thickness.
Also cut it to the required length.
3. Cut out small pieces
Remove knots and cut into a flat plate of a certain size using a four-sided planer.
4.Dry distillation (carbonization)
Bamboo pieces are carbonized at a constant temperature,
pressure, and time.
By carbonizing, it is possible to prevent insect damage (kikui
insects), and as a by-product, the color of bamboo can be
changed by adjusting the temperature.
This process is all controlled by computer.
veneer
1.Small piece finishing processing
Use a planer to cut the thickness of bamboo pieces into boards
with high precision.
This is a very important process because the surface precision
at this time greatly affects the quality of the veneer. We
actually select each one by hand.
2. Small block adhesion
Because veneer wood has a very high moisture content, moisture-curing adhesives are used instead of regular adhesives.
3.Large block adhesion
Stack the small blocks in both the width and height directions
to a size that allows for the specified size of the veneer.
Make sure that the colors etc. do not look out of place during
this process.
Veneer (vertical lamination/horizontal lamination)
1. Small block adhesion
Bamboo is a very hard material and cannot be sliced
​​like regular wood.
The know-how gained through many years of research is utilized
in cutting tools.
*The side where the knots are less visible is the vertical
slice.
2.Drying
When sliced, the moisture content is around 90%. In this condition, mold will grow, so dry it using a high-frequency dryer until the moisture content is below 10%.
3. The veneer is completed
The veneer is completed.
Vertical lamination has narrower spacing, giving it a more
modern look that goes well with Western styles.
Horizontal laminations are widely spaced and are sometimes
called Hira laminations. It has the characteristic that it is
easy to express the expression of knots and goes well with
Japanese style.
For details on veneers, please see “Bamboo veneer and bamboo
plywood”.
sawing board
1.Drying
For veneers, it is important to keep the moisture content high, but for flooring and sawn boards, it is important to lower the moisture content.
2.Small piece finishing processing
Use a planer to cut the thickness of bamboo pieces into boards
with high precision.
Surface accuracy at this time is very important for product
quality.
Grinding board (vertical lamination/horizontal lamination)
1. Small block adhesion
The bamboo pieces that have been processed in the previous process are carefully sorted and glued together to ensure that the colors are consistent.
2. The sawing board is completed
It is naturally dried in a curing room to a moisture content of 10% or less.
For details on flooring materials, please see “Bamboo
Flooring”.
For details on fittings, etc., please see “Bamboo fittings and
bamboo products.”